There are several signs that may indicate that your bucket cylinder assembly needs to be replaced or repaired.
Here are some common signs to look for:
Leaking fluid: If you notice hydraulic fluid leaking from the cylinder assembly, this may indicate that the seals or other components are damaged and need to be replaced.
Reduced performance: If you notice that the bucket or other attachment is not moving as smoothly or as quickly as it used to, china BUCKET cylinder assembly supplier this may indicate that the cylinder assembly is worn or damaged.
Excessive wear or damage: If you notice that the cylinder assembly is visibly worn or damaged, such as dents, cracks, or rust, this may indicate that it needs to be replaced.
Unusual noises: If you hear unusual noises or vibrations coming from the cylinder assembly, this may indicate that the components are worn or damaged and need to be repaired or replaced.
Pressure loss: If you notice a loss of pressure in the hydraulic system, this may indicate that the cylinder assembly is leaking or not functioning properly.
If you notice any of these signs, it’s important to have the bucket cylinder assembly inspected and repaired or replaced as soon as possible to avoid further damage or failure. Regular maintenance and inspection of the cylinder assembly can help prevent problems and ensure proper operation of your heavy equipment.
How often should I have the cylinder assembly inspected?
The frequency of cylinder assembly inspections depends on several factors, including the type of heavy equipment, the operating conditions, and the manufacturer’s recommendations. In general, it’s a good idea to have the cylinder assembly inspected at least once a year or more frequently if the equipment is used frequently or in harsh environments.
Here are some factors to consider when determining how often to have the cylinder assembly inspected:
Operating conditions: If the equipment is used in harsh environments, such as dusty or sandy conditions, or if it is exposed to extreme temperatures or weather conditions, it may require more frequent inspections.
Frequency of use: If the equipment is used frequently or for extended periods of time, it may require more frequent inspections.
Manufacturer’s recommendations: The manufacturer of the heavy equipment may provide recommendations for how often to inspect the cylinder assembly. Be sure to follow these recommendations to ensure proper operation of the equipment.
Signs of wear or damage: If you notice signs of wear or damage to the cylinder assembly, such as leaks, reduced performance, or unusual noises or vibrations, it may indicate that the cylinder assembly needs to be inspected or repaired.
Overall, regular inspection and maintenance of the cylinder assembly can help prevent problems and ensure the safe and efficient operation of your heavy equipment. Be sure to follow the manufacturer’s recommendations and consult with a qualified technician if you have any concerns about the condition of the cylinder assembly.
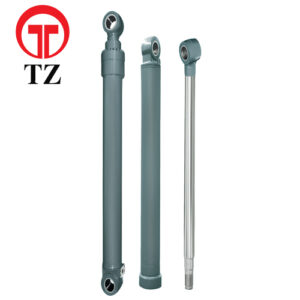